Navigating Quality Management: Distinguishing NCR, CAPA, ECO, and MRB
Quality Management Systems (QMS) are integral to any organization striving for consistent improvement in their operational processes. These systems comprise several key components, each serving a unique purpose: Non-Conformance Reports (NCR), Corrective Actions and Preventive Actions (CAPA), Engineering Change Order (ECO), and the Material Review Board (MRB). Understanding the distinctive roles and interplay of these elements is crucial for efficient and effective quality management.
Understanding Non-Conformance Reports (NCR)
The NCR process is the first line of defense in the quality control systems. It initiates when a product or process fails to meet the predefined standards or expectations. It involves identifying, documenting, and reporting these deviations or non-conformities in a structured manner.
Every non-conformance reported via an NCR is evaluated based on its severity, impact on product quality, and potential risk to the customer. This process aids organizations in understanding the issues that plague their operations, providing crucial data for further problem-solving mechanisms, such as CAPA.
The Role of Corrective Actions and Preventive Actions (CAPA)
CAPA systems step in where NCRs leave off, taking the quality assurance strategies a step further. Once an NCR identifies and documents a problem, the CAPA process targets the root causes of these non-conformities. It's a two-pronged approach:
Corrective Actions: These are reactive measures taken to eliminate the causes of an existing nonconformity or defect to prevent its recurrence.
Preventive Actions: These are proactive measures designed to eliminate the causes of a potential nonconformity or defect to prevent its occurrence.
Effective CAPA processes contribute significantly to reducing manufacturing issues, improving product quality, and enhancing customer satisfaction. It ensures organizations don't just 'firefight' problems as they arise, but they implement strategies to prevent such problems from recurring or even occurring in the first place.
Diving into the Engineering Change Order (ECO)
Change is inevitable in any manufacturing process. As a result, managing change effectively becomes pivotal to maintaining quality standards and meeting customer requirements. The ECO process provides a structured method for proposing, reviewing, approving, and implementing changes in a product's design or process.
Whether these changes are prompted by an NCR finding, a CAPA initiative, a design improvement, or a regulatory requirement, ECO ensures they are well-documented, justified, reviewed, and approved before implementation. It keeps all stakeholders in the loop, maintains design control, and ensures traceability of changes, thus playing a crucial role in quality management.
The Material Review Board (MRB) and Its Importance
The MRB is a cross-functional team that takes the reins when non-conforming materials or products come into the picture. They bear the responsibility of deciding the disposition of these materials. They examine whether these materials can be accepted 'as is' for use, need to be reworked or repaired, or should be scrapped.
The MRB's role is particularly significant in cases where the non-conformity doesn't pose a significant quality or safety risk, and it might be more cost-effective or efficient to use the material as is. The MRB works hand in hand with the NCR process, as it typically reviews the non-conformities highlighted by NCRs.
NCR, CAPA, ECO, MRB: A Symphony of Quality Management
The interplay between NCR, CAPA, ECO, and MRB within quality management systems is a symphony of continuous improvement. Each component, with its unique focus and function, harmonizes with the others to create a robust and efficient system that upholds quality, maintains compliance, and drives customer satisfaction.
Understanding the distinctive roles of these elements and managing their interactions effectively can supercharge your organization's quality management efforts. Remember, a quality management system is not just about addressing problems or managing changes - it's a strategic tool that, when used effectively, can drive operational excellence, reduce costs, improve customer satisfaction, and give your organization a competitive edge.
As you navigate through the challenges of quality management, keep these differences and interactions in mind. Use each tool for its intended purpose and make them work together in harmony. After all, the ultimate goal is to ensure consistent product quality that meets or exceeds customer expectations. In the world of manufacturing and quality assurance, there is no greater success than this.
Refrences
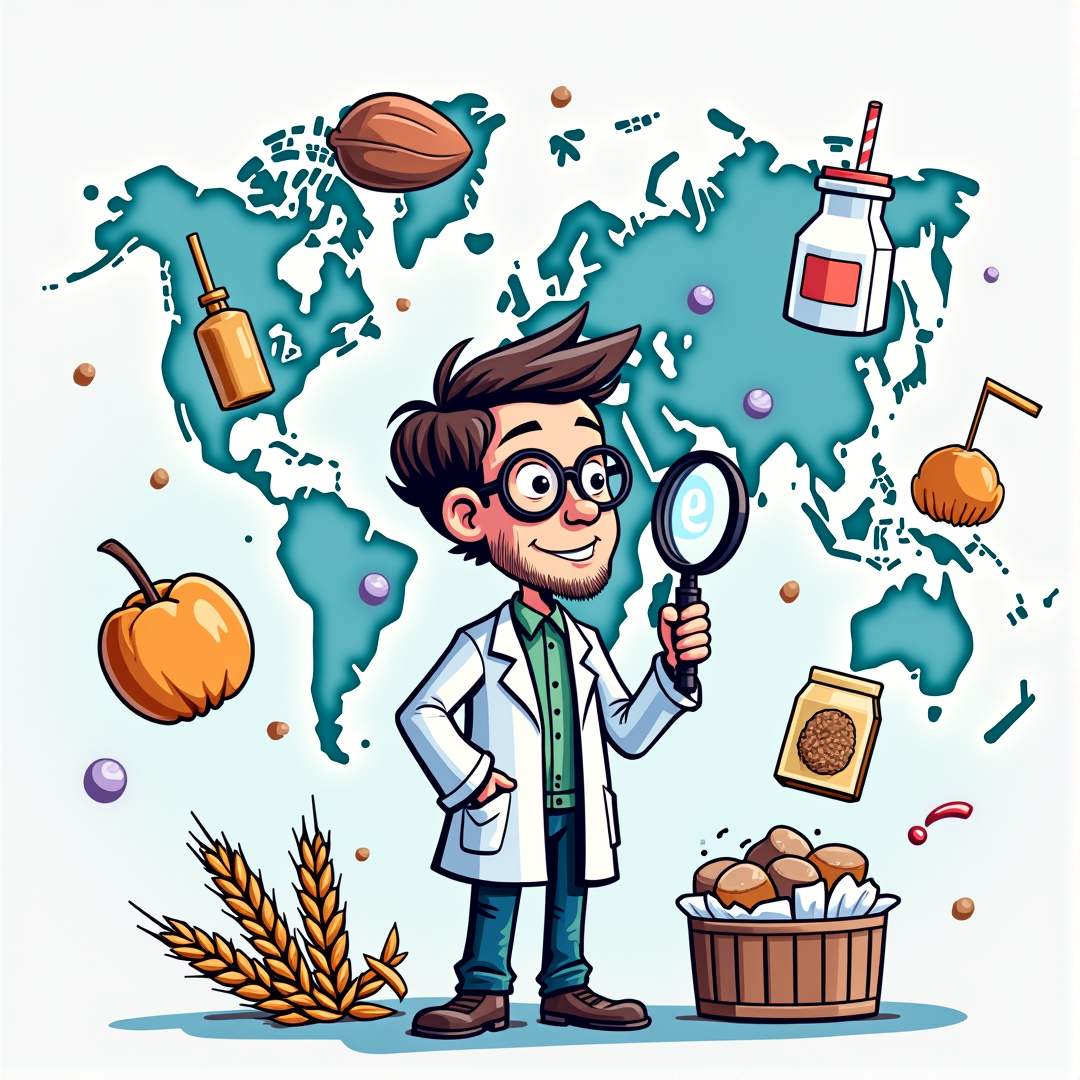
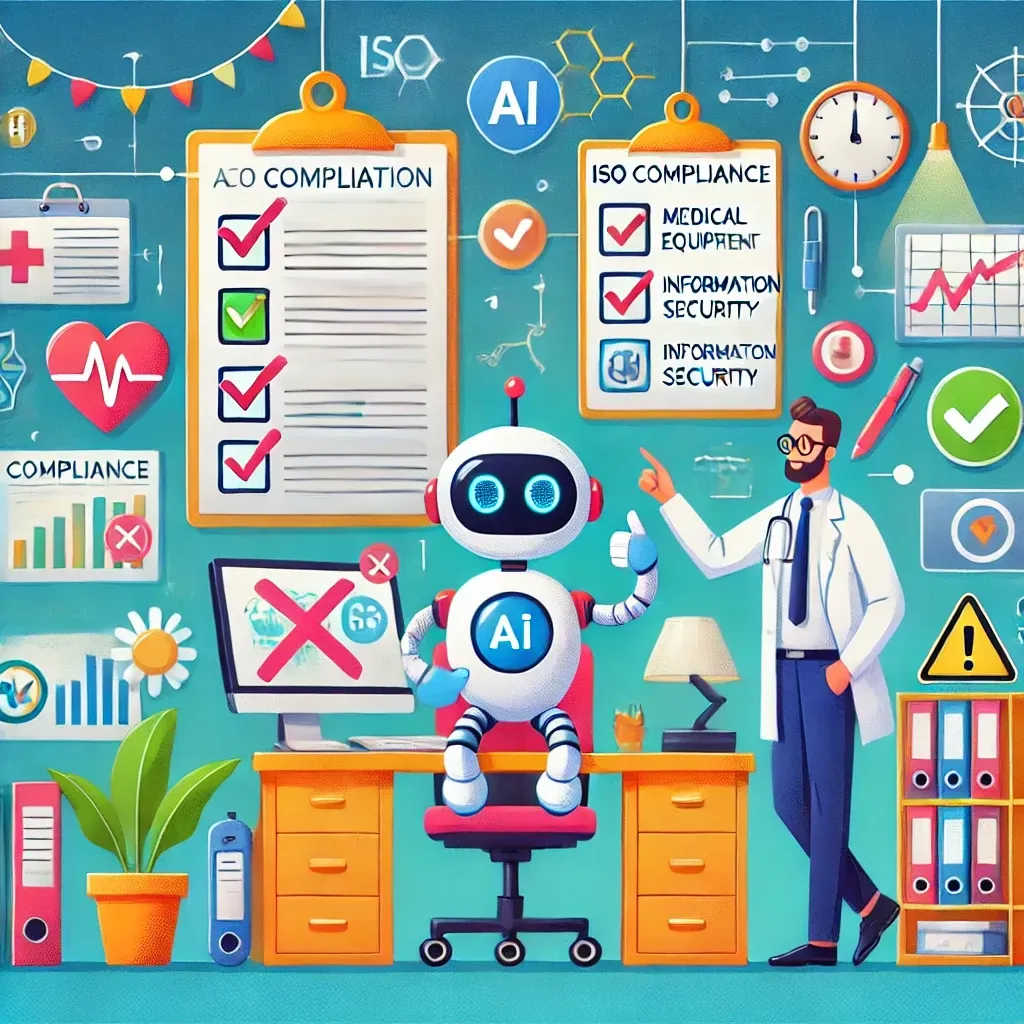
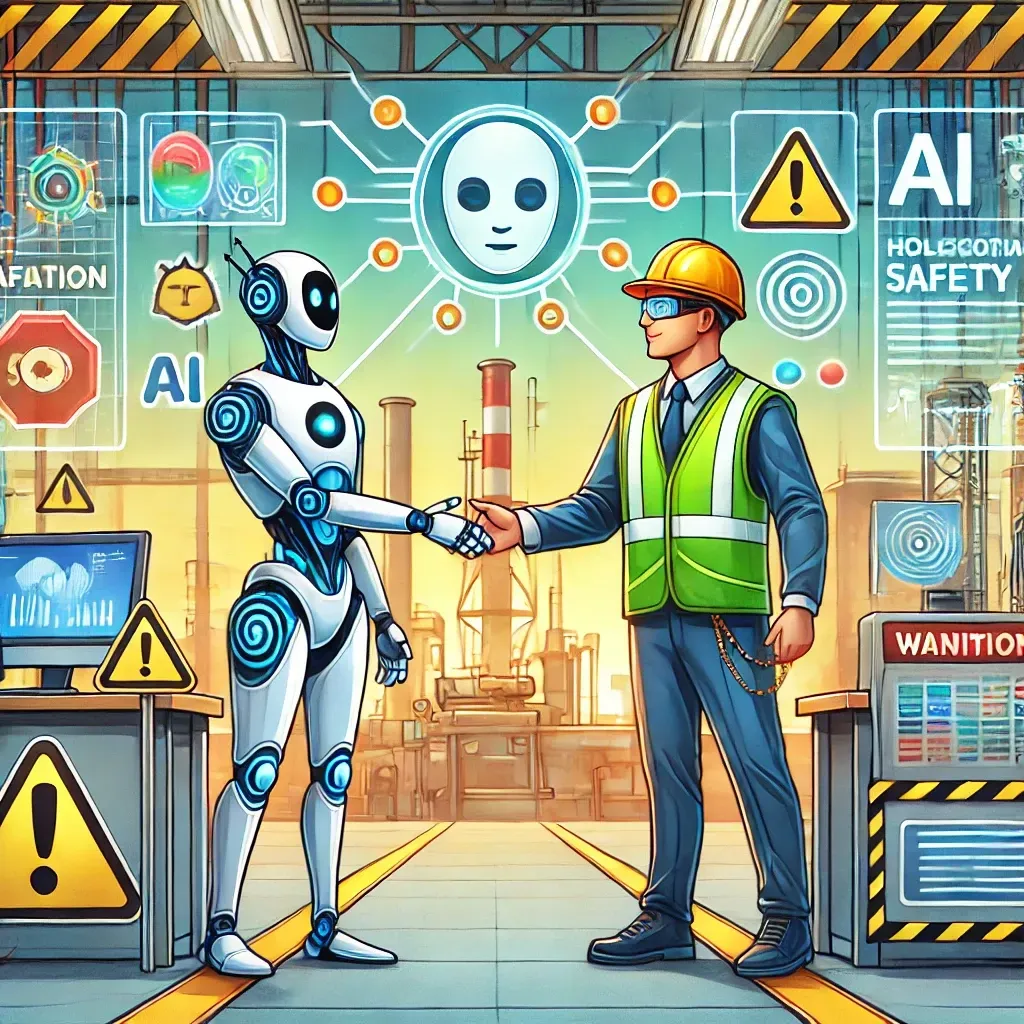
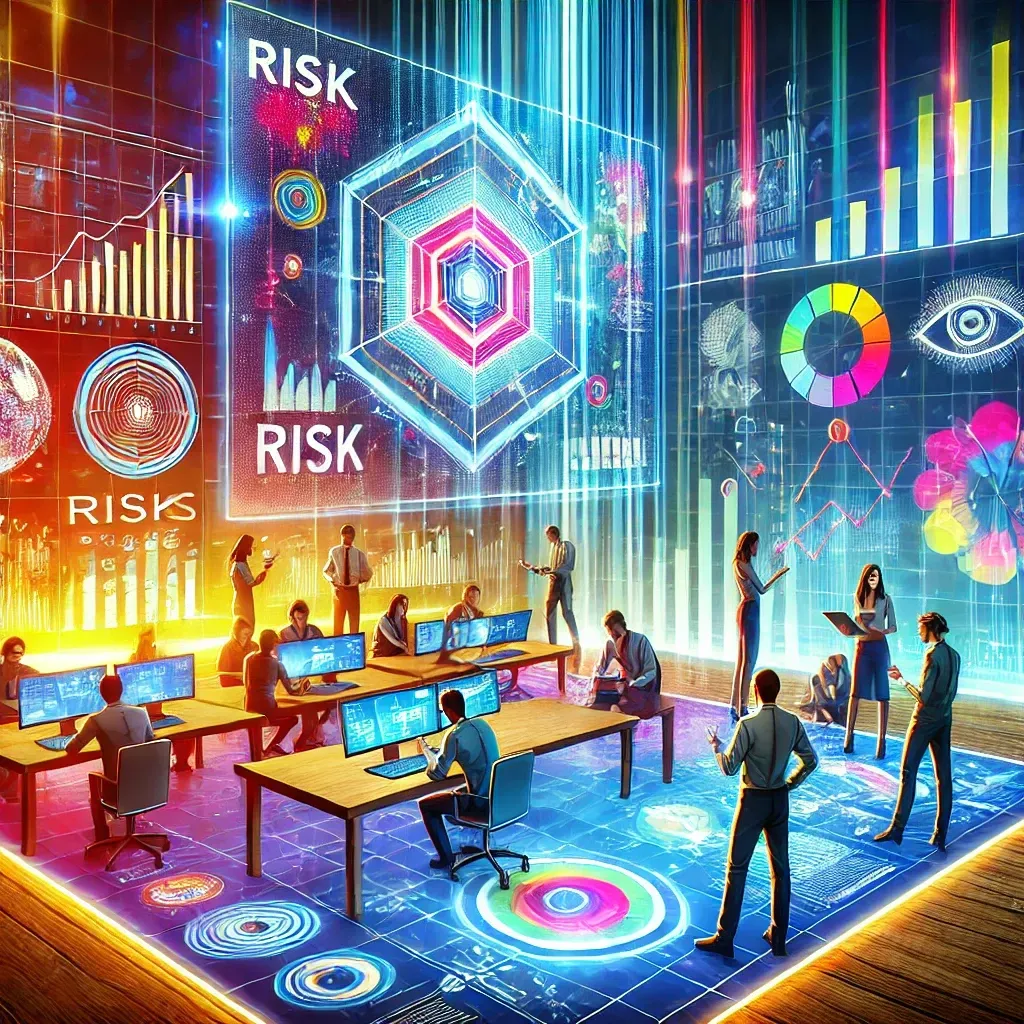
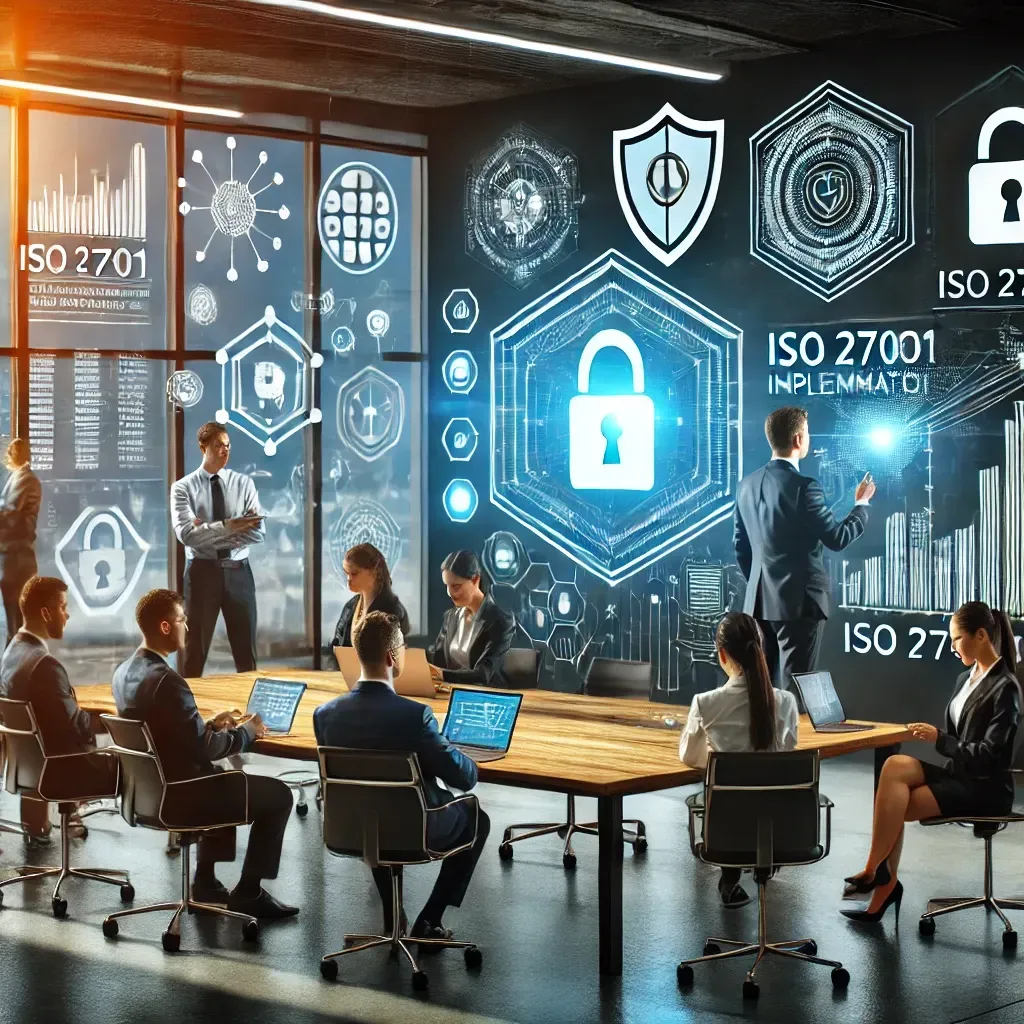
